In Chicago, 1 in 5 households experience hunger with 1 in 4 children in the city specifically experiencing hunger. In mid-2022, I started working on the design of an efficient and compact vertical hydroponics tower system that can be utilized to fight urban hunger. I started my design on paper and researched the top players in the hydroponics industry to find what they are doing wrong, what I can improve, and what I can fix. The technology is simple but no one is seemingly maximizing efficiency in their systems. With the assistance of a civil engineer to help with various questions related to structural integrity and cost assessment; I was able to draft a planned and cost-efficient steel building frame to house growing units made of entirely recycled materials.
Below, you will find an architectural render of the Vertical Hydroponics Tower frame and unit placement in Unreal Engine 5 that I am preparing for a demonstration to officials from the City of Chicago. Soon, I will add a VR example of how the interior of the tower will function.
Here is the architectural rendering of the framework behind the lightweight Vertical Hydroponics Tower alongside the same tower removed from its placement on top of an example of an older 5-story construction.
This rendering and writing are being created as a visual reference guide for the Vertical Hydroponics Tower System I have created and to explain the reason for such a design.
The tower can be constructed outside of urban environments; however, the design intent is for the Vertical Hydroponics Tower to be placed on older buildings with existing and stable foundations that will be reinforced.
The Vertical Hydroponics Tower system is designed to be built and constructed in a fraction of the time compared to other sky scrappers and even mega parking garages. My main plan in gaining my ideal funding goal is to establish the manufacturing framework for all construction pieces needed for the tower's frame and grow units. Taking control of the manufacturing process will not only prevent price gouging on what could easily solve hunger in some urban environments; doing so will also provide more jobs to the City of Chicago, my home.
A single Vertical Hydroponics Tower as designed in the architectural renderings is set to run on a 42-employee roster year-round with an employee operational cost of 2.4 million USD a year with hourly workers earning a living wage by Chicago standards while receiving benefits regardless of a full-time weekday employee or a half-time weekend employee status. The low employee cost will be maintained through advanced automation of facility monitoring, produce collection, and other systems. Each tower will present local municipalities with jobs and even economic growth over time.
Over time, community members that come to get free produce and that will be given free produce through planned partner food pantries will start to return money to the economy. Depending on the yield and amount of produce in weight we can successfully distribute to those in need, 5 Vertical Hydroponics Towers of the same size as rendered here can double the 10-year investment put into them if we count this positive flow of money back into the economy. A population where households will have extra money per person will direct that money they would have spent on produce back into the local and national economy, presenting long-term positive effects.
Below, there is another rendering visually demonstrating the modularity of the building with further explanation.
The tower is designed to sit on top of Caisson Foundation Cylinders supported by a standard Pile Foundation base. The chosen foundation design is to add the needed support for a tower that will be tall enough that it will need to sway due to high winds affecting structural integrity.
This will allow for the lightweight steel frame to be placed on this foundation when an existing building is used as the base for the tower; reinforcing the new construction with the Caisson support while also verifying the integrity of and re-inforcing existing Pile Foundations.
While not featured in any rendering, the tower will also make use of cable support similar to how large radio towers are given more stability.
At the top of the modular construction, there will rest the water tanks that will feed the water to the tower through low-energy usage pumps and gravity.
The water tanks being placed at the top of the tower also help with keeping the building stable during high winds and necessary sway. The use of water tanks/water ballast on top of tall towers is common in the construction of modern sky scrappers to ensure stability.
Making use of the light load the growing units present, each frame section will be conjoined using a mix of standard skyscraper welding techniques and bolting of specific girder supports to allow for an economically friendly deconstruction and unit swapping in the given events.
Denoted by the red-orange color, you will see the location of what will act as the air intake and temperature regulator for each unit.
The compartmentalization and per-unit control of air intake and temperature are simply so we can have not only multiple seasons occurring throughout the tower at once per unit; but so we can also grow foods unique to environments that people from Chicago may never have tried.
On top of just growing food, the possibility of more units being added and used for food research stands high; having units with such environmental control will help us attract a variety of universities for example wishing to grow experimental crops that are usually temperamental with the conditions they are grown in.
Fluid Dynamics Models are also being used in specific aspects of the growing unit's planning to allow for maximum and dynamic airflow; allowing us to control wind speeds in units individually and even to have various wind speeds in one unit. Doing specialized air and wind control will allow us to grow plants for example that will strive in higher winds due to producing greater produce yield when stem strengthening growth is encouraged by wind speed.
Now, the design of the units themselves is made to maximize the use of space and advanced physics more than existing vertical hydroponics setups from major companies in the hydroponics industry. Eden Green Technologies, for example, is utilizing over 11,000 square meters of warehouse space just to grow a projected 1.8 million pounds of produce in a year in their project with initial start-up costs nearing almost 50 million dollars USD.
With my system, a framework design holding 4 units on each floor with 12 floors total will have 25,392 Square Meters(23m x 23m approx of space per unit) of growing space. Utilizing grow racks as tall as what is present in Eden Green Technology warehouses, we will be able to provide just under 4.0 million pounds of produce a year per tower designed as depicted in the renderings; without any research to start advancing yield amounts genetically. All of this at a fraction of the cost; just about 30 million USD would start one Vertical Hydroponics Tower and can also start the needed research to help make GMO high-yield produce designed for our system. With the help of research universities and more scientists; we can easily increase the yearly yield from a tower like the one described and pictured above in no time.
It has to be mentioned that the most costly aspect of this project is the steel frame construction that houses the growing units. I have sought to minimize this by utilizing a modular building design so that we can also localize the assembly of steel girders into frames. Creating one 52mx52m frame and transporting it in a nearly direct path to the tower construction sites to be raised and slotted into place on the tower is ideal. Most likely, the frame will be partially constructed in quarters to be delivered to the construction site. A similar method of local production and direct construction site delivery will be used for the individual growing units if the production of the units can be localized completely utilizing available materials for recycling.
The use of old buildings, or Upcycling buildings, that might be found disused in areas where there are rising and present food security issues are complex. Using old buildings with community memories will help present something new with something familiar to the community versus tearing a historical building; maybe even causing disdain among local residents.
Another advantage to using an existing building; the produce that is grown in the Vertical Hydroponics Tower will have a quick trip to a designated area where it can be prepared to distribute to the people in need of it soon after harvest. A building just below the tower means no need to freeze the grown produce or do anything that might damage nutritional value. As well as providing existing and cheaper space than new construction space; the remainder of the unused and unplanned for space can be used for community events and even vendor spaces to lift up local community businesses and artists.
Focusing these towers directly in communities where they will be most needed also prevents the issue of the savings from the program being spent just to get to the tower for free produce. For example; spending on transportation just to get free produce still leaves the community with a cost in the end despite the savings. So building towers where they can easily be reached by the most vulnerable communities means savings caused by the project will go into the local economy versus a corporate transit entity with a city contract. We have to preserve the positive economic effects by making sure we place the Vertical Hydroponics Towers where they will have the most effect and the most reach.
Imagine the possibilities of community spaces that can be created here too if we really focus on bringing something that a community can gather around. One of my favorite plans for the upper interior floors of a converted building is to set up a hydroponics fruit tree system for the community; to bring unique fruits into the hands of the community this tower exists to help.
Even with a focus on compact and efficient design for the sake of urban use and manufacturing; I made these renderings as well to show that the towers will still leave enough room for properly protected individuals to move through the rows of grow racks comfortably. This is only a rough rendering of the interior to represent the space; a better interior reference is being created for the VR Sample Experience being created.
The overall size of the unit and layout are also simple so if produced, we can maintain minimal production cost on top of using recycled materials for the units; allowing for more configurable productions if needed without having complex cost increases. Using advanced lighting techniques; recycled reflective materials will play a large role in helping to increase produce yield.
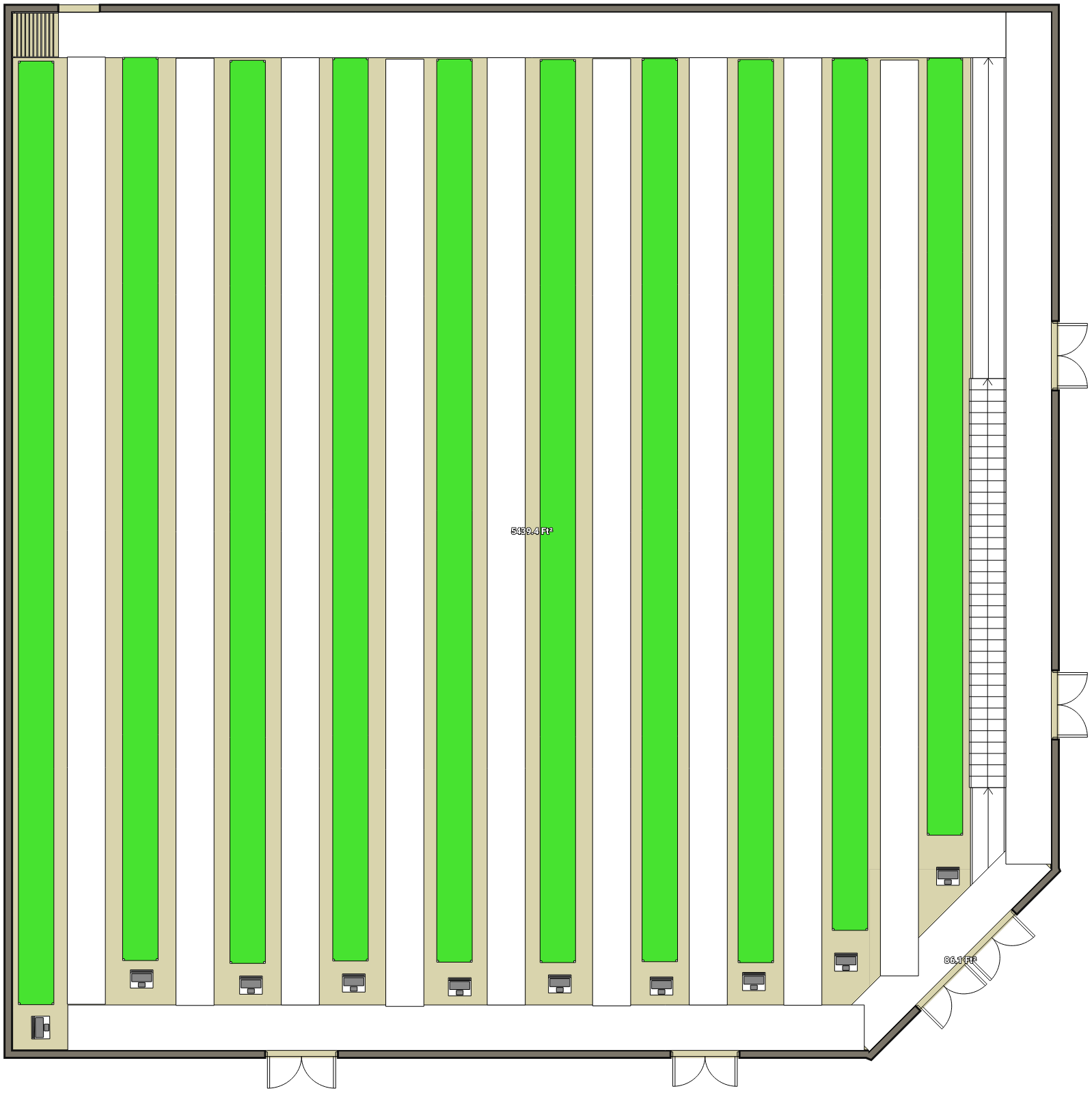
There are challenges to a project like this, the greatest being that it is ambitious. To be able to plan something like this and execute a plan like this would take relentless effort and only the right people. I believe I have started to acquire the right people already for this project, and I believe I can find a location for the first tower with that ambition in mind.
VR Experience Sample and Professional Infographics Coming Soon